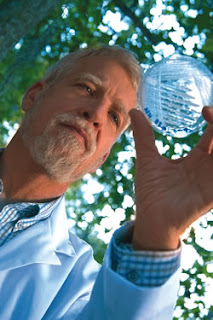
Two weeks ago, Lonnie Ingram came and gave a talk here and I had a chance to take some notes which I will share with all of you as well as some of my thoughts.
Introductions...
Most fuel in the US is produced domestically. However we still import lots of oil for fuel and coproducts (like solvents).
Biomass is used in three processes right now US Whiskey (from corn), Brazillian Rum (from sugar cane) and University of Florida's Tequilla process (from lignocellulose, hexose and pentose aka starchy stuff like switchgrass ).
Production from cellulose requires acid/base pretreatment which creates inhibitors to cellulases. Usually by dropping the starch in a tub of acid or blowing it up. Then you can mix it in with your bacteria or enzymes in the fermenter.
1. Engineering Organisms for increased yields: Zymononas mobilis
By mucking around with this organism they were able to reduce the net energy loss into CO2 making the fermentation process more efficient. Then they eliminated competing reactions and then used increasing biomass as a selection marker for better ethanol production in directed metabolic evolution.
2. Increasing ethanol tolerance, the more the bug can stand the better for production. I don't remember any publication work that he mentioned.
3. Since there are multiple sugars in starchy sources its important to get the most out of them and he talked about the sugar co-utilization of xylose and glucose, and how it can be improved with mutations to methylglyoxal synthase.
4. Deconstruction and inhibitors: by using cellulases they showed how to skip the expensive liquid solid separation and wash steps and just go pretreatment (see above)->fermentation-> purification (getting your liquor out of the gunk). Now they just need to have the bacteria operate at higher temperature and pressure to get the cost down. The three major compounds which are extracted from the starch and function as inhibitors were furfural from hemicellulose (which Quaker Oats produces from corn hulls for use as solvent or in resins), acetic acid and hydroxymethylfurfural.
The first thing they did was look for a furfurol reductase using mutant screening. They found that sulfur relieved some of the furfural inhibition. Eventually discovering CysIJ reductase and that furans inhibit growth by depleting the NADPH pool.
6. Fermentation for co-production:lactic acid is a co-product in fermentation. They worked with a company to produce it for use in poly-lactic acid (PLA) for the production of bioplastic. Pediococcos IdhL. There is a big need for the production of D and L lactic acid to blend for bioplastic production.
7. Succinate is a key building block (on the DOE top 10) and work done by Xueli Zhang looked at improving yields through flipping pathways around to produce succinate from CO2.
He lastly mentioned how to promote synergy in the way plants are setup taking the waste CO2 from the fermentation part of the plant and producing succinate in another, I would expect to see networks like these in the world future biorefineries.
First Gatorade and now cellulosic bioethanol. The University of Florida really knows how to do technology transfer! Its really great to see academics pushing new tech into the private sector. This makes me cautiously optimistic about the chances of taking some tech that I develop as a grad student or postdoc to the market through a startup. I don't have anything yet, but I definitely have some ideas up my sleeve. Mr. Ingram failed to mention his funding sources but the idea of industry working with academics sounds like a good alternative source of research funding from the NIH/NSF.